Short description of the project
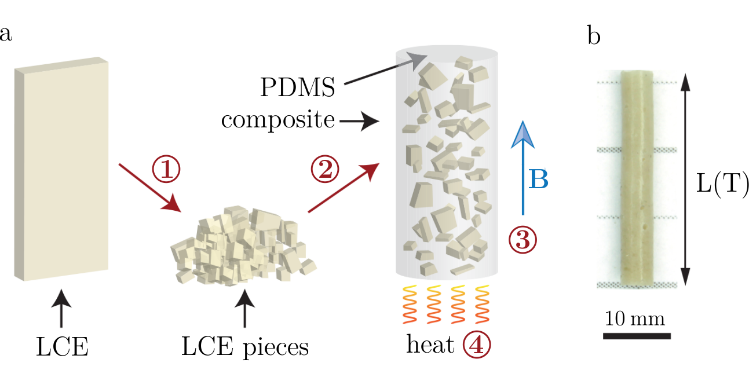
The development of soft flexible materials with morphing and shape-programmable abilities is essential for technological progress of soft robotics, biomechanics, and flexible electronics. However, morph-on-demand materials remain a rather elusive class of smart materials. Shape-programmable matter capable of transforming between three-dimensional shapes in response to external stimuli such as light, heat, electric and magnetic fields is a class of active materials whose geometry can be controlled for performing tasks beyond the operational scope of conventional machines or robots. In this project, we are proposing the development of a method to produce a new generation of 3D-printable soft material with anisotropic response. The material will be based on the recently developed polymer dispersed liquid crystal elastomers (PDLCE). Such composite material consists of thermomechanically active liquid single crystal elastomer (LSCE) microparticles, dispersed and oriented in a crosslinked polymer matrix. The particle orientation can be spatially modulated using an external magnetic alignment field over the composite volume, resulting in custom-tailored, temperature responsive shape changes of the specimen.
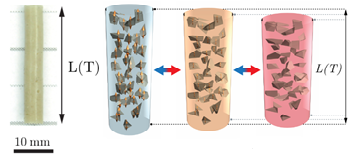
We have recently devised a method of producing a suspension of anisotropically shaped LSCE microparticles with their liquid crystal ordering and consequently, direction of thermomechanical actuation, aligned along the particle’s longer axis. Anisotropically shaped LSCE particles can thus be oriented using simple laminar flow, present during deposition while 3D printing the material. The use of the state-of-the-art robotic hand with a mounted polymer dispensing unit, will enable us to precisely control the imprinted thermomechanical anisotropy, by exploiting the robotic hand’s six degrees of freedom of movement in order to deposit PDLCE voxels at arbitrary angles. The developed 3D printable ink will be used to print a tube capable of peristaltic movement, triggered by consecutive heating and cooling of the specimen via incorporated heating wires or by UV/ microwave irradiation absorbing nanostructures additionally functionalizing the LSCE composite. The realization of a 3D printed peristaltic tube will demonstrate the applicative advantages of our printing method and of the PDLCE 3D printable ink, by producing a specimen with complex morphing abilities that cannot be achieved by any of the currently developed additive manufacturing technologies.
Work programme
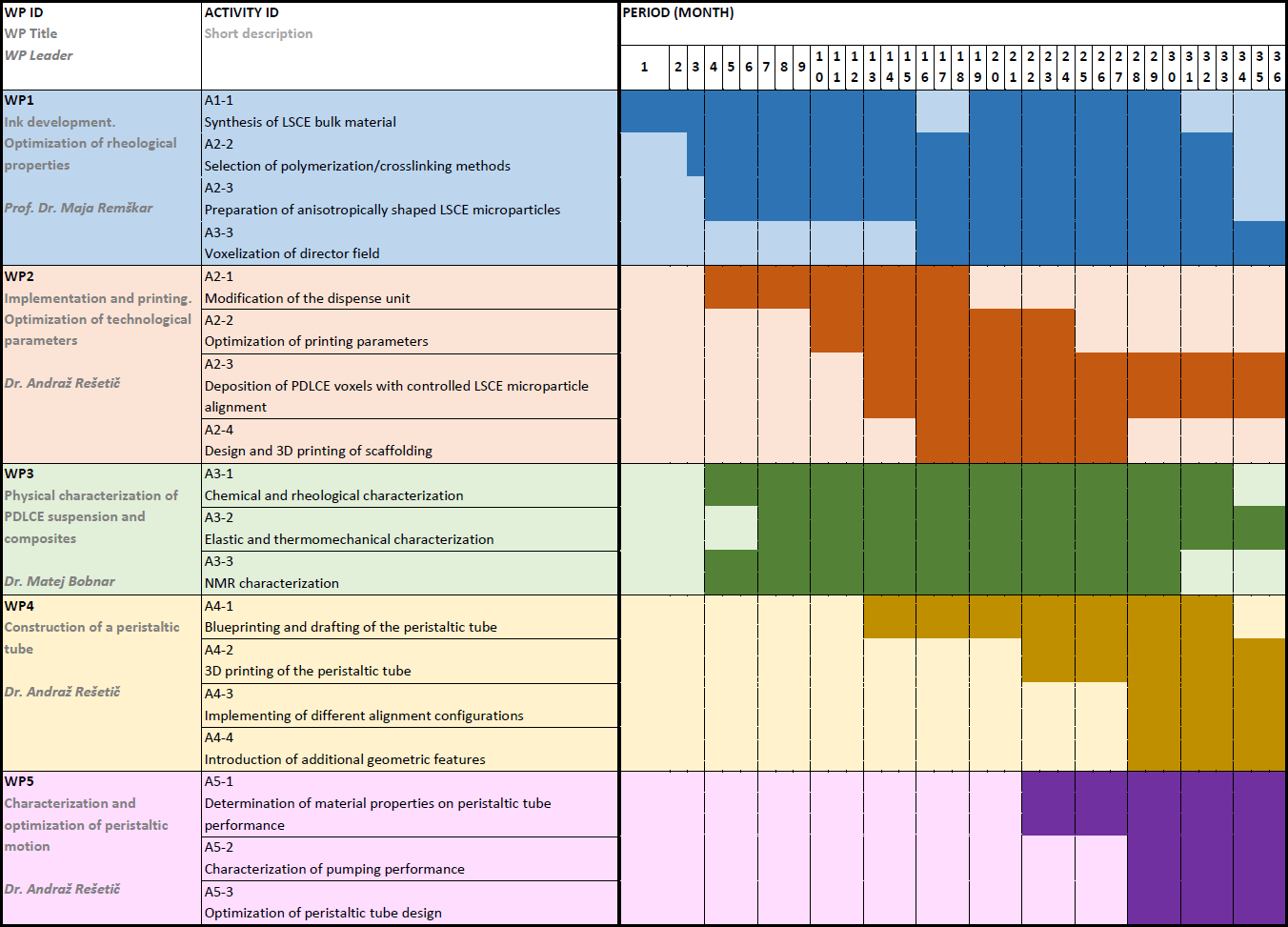
Work package 1: Ink development. Optimization of rheological properties
We shall select a suitable combination of (i) conventional elastomer, (ii) liquid crystal elastomer (LCE) and (iii) curing method in order to prepare 3D printable ink, which will be employed for producing thermomechanically functional PDLCE composite material. The choice of conventional elastomer medium will be based mostly on its rheological properties. Filler material, in our case LSCEs, will be based on side-chain and main-chain mesogenic constituents. Side-chain LSCEs exhibit lower Young’s modulus (≈ 100 kPa), therefore they can be easier mechanically deformed (important in the pre-shearing process), but exhibiting lower thermomechanical response (≈ 50 % of contraction) in comparison to main-chains (typically ≈ 200 % contraction). The anisotropic LSCE microparticles will be produced by shearing the PDLCE suspension between two parallel plates inside a temperature controlled chamber.
Work package 2: Implementation and printing. Optimization of technological parameters.
PDLCE printable ink will be implemented to be used with a 3D printing robotic hand with a mounted dispense unit for extrusion of viscous polymer materials. The printing parameters like pressure, nozzle size, translational positioning, nozzle tilt and printing speed, are controllable and will be optimized for deposition of PDLCE suspension. The dispense unit will be modified to address the polymerization method used for the PDLCE ink, either by a heating element or by UV-light diodes. LSCE particles are expected to aligne under an orienting flow. Our two primary goals are (i) understanding the physics of mechanical deformations originating from spatially modulated particle alignment and (ii) creating the methodology for in-situ thermomechanical activation of conventional elastomer.
Work package 3: Physical characterization of PDLCE suspension and composites
R&D of effective elasticity, rheological properties, thermal response, thermodynamic as well as NMR characterization of the PDLCE suspension and ensuing 3D printed materials in all stages of preparation will be performed. The information on dynamic, thermodynamic, structural properties and interactions will deliver complete set of data for ultimate modelling and projecting final prototypes with tailored properties. Rheological measurements will be performed on both the PDLCE suspensions and cured PDLCE composite material in order to assess and characterize the choice of materials and PDLCE suspension/material parameters. The degree of liquid crystal ordering inside anisotropic LSCE particles will be determined via quadrupole-perturbed deuteron NMR spectroscopy.
Work package 4: Construction of a peristaltic tube
A prototype thermal peristaltic tube will be developed in order to demonstrate the potential of in-situ “writing” of the thermomechanical anisotropy frame, i.e. the direction of thermally induced mechanical deformation into the PDLCE actuating part of the printed peristaltic tube. The tube will be cylindrically shaped and made of sections with differently aligned thermomechanically active LSCE particles in order to mimic peristaltic motion. The deformations will be triggered by incorporated heating wires into the specimen.
Work package 5: Characterization and optimization of peristaltic motion
A method for characterization of the peristaltic tube properties will be devised. Peristaltic motion requires fast deformation rate and sufficient thermomechanical contraction/expansion to ensure a steady propagation of the transporting material. Special experimental setups will be constructed for monitoring the speed and degree of thermomechanical actuation. The efficiency of peristaltic motion will be determined by measuring the velocity and pressure of the expelled liquid. Design of the peristaltic tube will be optimized based on obtained results.
Project group members:
- Dr. Andraž Rešetič, project leader (SICRIS link)
- Dr. Boštjan Zalar (SICRIS link)
- Dr. Matej Bobnar (SICRIS link)
- Dr. Maja Remškar (SICRIS link)